How BMW is trying to modernize manufacturing
Jan 24, 2020
By Jenny Marc and Nell Lewis, CNN Business
Updated 12:36 PM ET, Thu January 23, 2020
Regensburg, Germany (CNN)On the outskirts of one of Europe’s best preserved medieval cities is one of the world’s most modern factories.The BMW group plant in Regensburg, Germany, manufactured approximately 320,000 vehicles in 2018. BMW says its use of technologies — from robotics to 3D printing to smart data analytics — meant it was able to cut the time needed to deploy new applications by 80% and reduce quality issues by 5%.
The plant — which was described as a “factory of the future” by the World Economic Forum — is at the forefront of what’s being called “Industry 4.0” — a new phase in the industrial revolution that focuses heavily on interconnectivity, automation, machine learning, and real-time data.

Smart factories like this one could add at least $1.5 trillion to the global economy in the next three years, according to Capgemini. And many more are coming: the consulting firm found that the manufacturers it surveyed in 2019 planned to create 40% more of these plants over the next five years.
High-tech car making
“A smart factory is characterized by a smart way of using new technologies, (and) new ideas to get innovations on a next level,” says Frank Bachmann, BMW’s Regensburg plant manager.There are more than 3,000 connected machines, robots and autonomous transport systems at the plant. A custom-made Internet of Things platform links these tools with materials and parts, which are given laser-printed labels at the outset — allowing information to be analyzed and tracked every step of the way.That means any problems in the supply line can be alerted. For instance, if the system detects strange noises, mechanics are notified, and the problem can be fixed immediately.
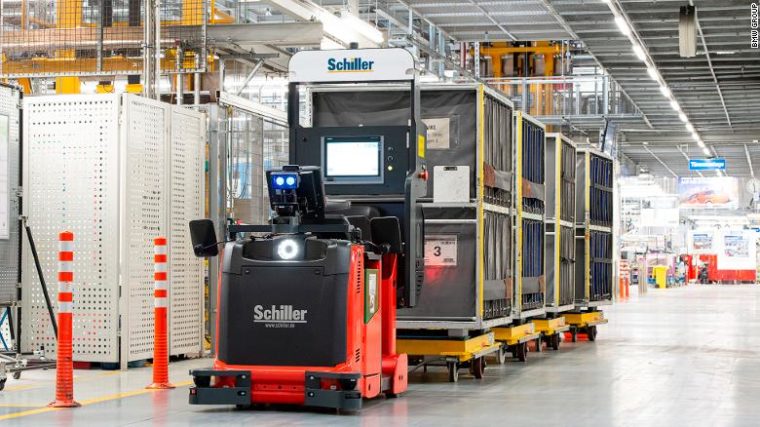
“We try to predict things, try to understand things in a reactive way, to make the future safer, easier and make even better cars,” says Bachmann.Bachmann believes the factory’s success is not down to one single technology, but how it integrates technologies with human workers.”A smart factory is driven by smart people,” he says.
Driving the industrial revolution
It is not the first time cars have been the driving force in modernizing manufacturing. Henry Ford created the first moving assembly line in 1913, which drastically cut the man-hours required to assemble a Model T car — from 12-and-a-half-hours down to six.But the next generation of manufacturing won’t just take place on the plant floor. It will happen on computers and in the cloud.This brings some additional challenges. Capgemini’s report found that despite the overriding positive outlook, manufacturers are struggling to scale up their smart initiatives, with just 14% characterizing their existing initiatives as “successful.”
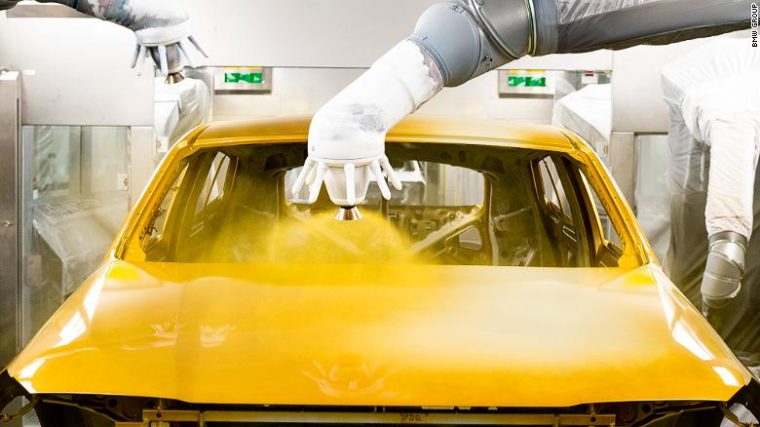
Enno de Boer, of consultants McKinsey & Company, also sees some hurdles to overcome. “Two of the biggest challenges facing manufacturers are around employee capability and scale,” he says.”There is a big skills gap to be addressed — 42% of industrial companies are reporting they are already experiencing a shortage of labor with 4IR [Industry 4.0] capabilities,” he adds.To reskill and upskill the workforce at scale, de Boer suggests manufacturers develop effective technological learning methods, such as gamification and VR or AR learning.
Original Article: https://www.cnn.com/2020/01/23/business/bmw-regensburg-smart-factory/index.html
Stay In Touch.
Subscribe to our newsletter and exclusive Leadership content.
We respect your privacy and won’t spam your inbox